Ultimate Overview to DTF Printing Methods for Spectacular Fabric Layouts
Embarking on the trip of understanding DTF printing strategies can open up a world of possibilities for producing aesthetically exciting fabric designs. As the textile market proceeds to advance, remaining ahead of the curve with ingenious printing techniques is essential. In this guide, we will certainly check out the detailed information of DTF printing, from grasping the fundamental basics to unraveling advanced color techniques that can elevate your designs to new heights. Stay tuned as we look into the nuances of choosing the ideal materials, perfecting the printing process, and conquering common obstacles to attain sensational results.
Understanding DTF Printing Essentials
DTF printing, a process that entails transferring layouts from a special film to textiles making use of heat and pressure, forms the foundation of fabric printing techniques. The very first action in DTF printing involves producing or selecting a style that will certainly be printed onto the textile.
As soon as the design is printed on the movie, it is after that thoroughly positioned onto the fabric, making sure correct positioning and positioning. The following essential step entails using heat and pressure utilizing a warmth press machine. This process triggers the dyes or pigments on the movie, creating them to sublimate and bond with the material fibers completely. The outcome is a stunning, resilient fabric layout that is washable, flexible, and resistant to fading. On the whole, understanding the fundamentals of DTF printing is essential for grasping this modern-day fabric printing technique.
Picking the Right Fabric Products
Having actually developed the fundamental principles of DTF printing methods for fabric styles, the next crucial consideration hinges on selecting the suitable textile materials to match this innovative procedure successfully. The success of a DTF print greatly relies on the compatibility between the selected fabric and the printing method. When picking textile products for DTF printing, it is important to take into consideration the fabric's structure, weave, and structure. Fabrics that work well with DTF printing include polyester blends, spandex, nylon, and other synthetic materials. These materials normally have a smooth surface area that enables detailed and vibrant prints. Additionally, the stretchability of these materials can suit the warm transfer process involved in DTF printing without misshaping the design. It is a good idea to stay clear of natural fibers such as cotton or silk, as they may not generate the same degree of print quality and toughness. By choosing the right textile products, developers can make the most of the potential of DTF printing to produce resilient and sensational textile layouts.
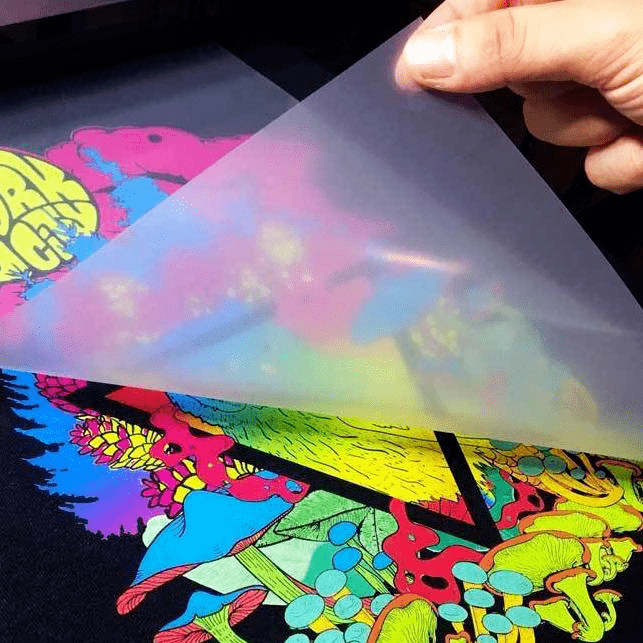
Understanding the Printing Refine
To excel in DTF printing strategies for fabric styles, mastering the printing procedure is important for attaining high-quality and regular results. The printing procedure in DTF involves a number of essential steps that require accuracy and interest to detail. Preparing the art work for printing is important. This consists of making certain the design is correctly sized and placed for the fabric. Next off, the design is printed onto a special DTF movie making use of a suitable printer with the best setups to achieve ideal shade vibrancy and quality (DTF Printing). As soon as the design is published, it is after that moved onto the textile using a warm press device. The temperature level, pressure, and period of warmth application must be meticulously regulated to ensure proper attachment of the layout to the fabric. Furthermore, mastering the peeling procedure after warmth pressing is important to avoid any damages to the layout or material. By developing each of these steps in the printing procedure, developers can regularly produce stunning and sturdy fabric styles with DTF printing techniques.
Enhancing Styles With Shade Techniques

Moreover, explore shade slopes can bring a feeling of activity and fluidness to the layout. By mixing shades flawlessly, a slope result can be attained, including a dynamic and contemporary touch to the fabric style. Furthermore, using color blocking methods can create striking and bold visuals by juxtaposing various strong shades in unique sections of the design.
Furthermore, integrating metal or neon shades can supply a attractive and unique component to the textile design, making it attract attention and show a sense of vibrancy. When strategically used, these color techniques can raise the general visual charm of textile layouts, making them much more captivating and remarkable.
Troubleshooting Common DTF Printing Issues
After exploring numerous color strategies to improve fabric styles, it is vital to attend to common DTF printing concerns that may develop during the production procedure. One typical concern is poor bond, which can result from incorrect healing times or temperature levels. To resolve this issue, ensure that the treating settings are accurate and that the glue used appropriates for the specific material being published on. An additional frequent difficulty is shade disparities, where shades might show up in a different way than anticipated. This can be triggered by inaccurate shade accounts or settings in the printing software program. To tackle Resources this, verify the my sources color settings and accounts to guarantee they match the intended design. Furthermore, concerns with photo clarity and sharpness can happen as a result of low-resolution photos or improper printing methods. To resolve this, constantly use top notch photos and readjust the printing setups for optimal clarity. By knowing these typical issues and applying the essential troubleshooting steps, you can enhance the overall quality of your DTF printed textile designs.
Verdict
In conclusion, grasping DTF printing strategies is necessary for creating sensational textile layouts. With practice and interest to information, one can produce unique and lovely textile styles making use of DTF printing techniques.
Layouts))))
DTF printing, a process that includes moving designs from a special movie to textiles utilizing warmth and pressure, forms the structure of fabric printing techniques.Having established the fundamental concepts of DTF printing techniques for textile layouts, the following crucial factor to consider exists in selecting the proper fabric products to match this cutting-edge process successfully. By picking the best fabric products, designers try here can maximize the capacity of DTF printing to develop lasting and magnificent textile styles.
To succeed in DTF printing techniques for fabric designs, grasping the printing process is essential for accomplishing top quality and constant results. DTF Printing. By refining each of these steps in the printing process, designers can regularly create long lasting and sensational textile styles with DTF printing methods
Comments on “Mastering DTF Printing: A Comprehensive Overview to Direct-to-Film Techniques”